41
05.10.20
Origine et évolutions des spécifications et normes pour les sols industriels
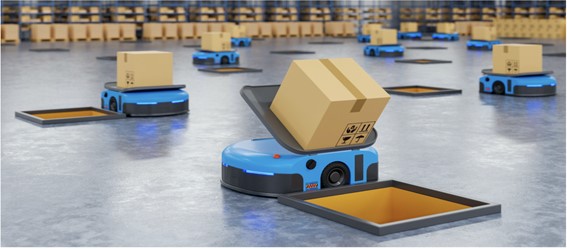
Publié le 5 Octobre 2020
« La science ne cherche pas à énoncer des vérités éternelles ou des dogmes immuables. Loin de prétendre que chaque étape est définitive. Elle cherche à cerner la vérité par approximations successives » B. Russel – Mathématicien – Prix Nobel
LES ORIGINES
Il fut un temps où la conception et la construction de sols industriels étaient simples et rudimentaires. Si les charges sur la dalle étaient légères à moyennes, 15 cm de béton et une seule nappe de treillis. Si les charges étaient lourdes, réalisation d’une dalle de 20 cm d’épaisseur avec double nappe de treillis soudé.
Les entreprises spécialisées en sol industriels n’existaient pas encore et la construction était généralement allouée dans le lot général du gros œuvre. Au cours des années 1970, les choses ont commencé à changer. Des méthodes de construction développées avec l’adoption du dallage monolithique avec coulage en déversement direct, permettant de couler et finir de plus grandes surfaces en une seule journée. Certaines entreprises se sont spécialisées, en premier lieu aux États-Unis, et ont commencé développer une compétence reconnue. À mesure que les surfaces quotidiennes augmentaient, le risque augmentait également.
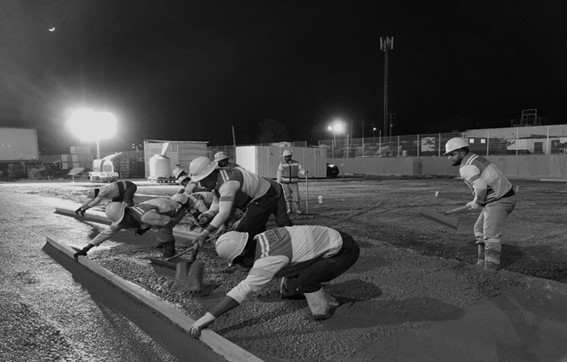
La chaîne d’approvisionnement d’un bâtiment industriel est complexe, plusieurs parties prenantes ayant chacune leurs propres intérêts.
Les entreprises de sol sont en bout de chaîne et souvent, toute excuse est utilisée pour que le paiement soit retenu contre eux. Si la fissuration inhérente au procédé est pourtant considérée comme problématique, le second critère de plainte concerne la planéité.
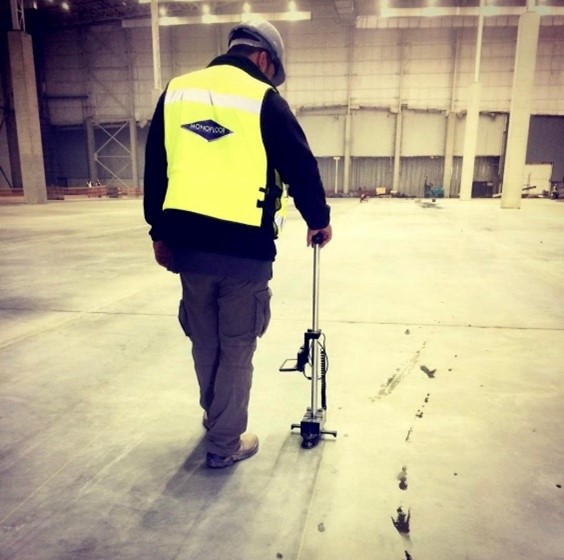
Afin de se protéger, ce secteur en plein essor des entrepreneurs de dallages en béton avait besoin d’un moyen de définir les propriétés de surface contractuellement.
En 1979, Allen Face a développé le système de numérotation de planéité du sol, plus communément appelé numéros F, qui sera plus tard formalisé par l’ASTM1155. Désormais, la qualité pouvait être définie, mesurée (Dipstick®) permettant non seulement à l’entrepreneur d’être payé mais aussi au client de savoir ce qu’il obtenait.

Alors que les nombres F fonctionnaient bien pour définir les performances des dallages à libre circulation, les chariots monodirectionnels, travaillant dans des installations avec des rayonnages plus hauts et des allées étroites (VNA) avaient des exigences différentes et spécifiques.
Ceci a donné lieu aux critères Fmin, mesurés à l’aide d’un profilographe roulant, qui sont devenus la première spécification de mouvement défini.
En 1987, le British Standards Institute a publié BS8204 : 2. Ce document a défini des catégories de planéité à l’aide d’un test de règle. Peu de temps après, la Concrete Society britannique a publié sa première édition du rapport technique TR n ° 34, rassemblant des orientations pour la conception et la construction de dallages industriels. À peu près à la même époque, Somero a lancé sa Laserscreed® sur le marché, modifiant la construction des sols à travers le monde dans les années qui ont suivi. À l’exception du mouvement défini, où la construction à longues bandes est encore couramment utilisée, la construction en grand panneaux est devenue la norme. La Concrete Society a publié TR34 édition 2 en 1994, suivie par la suite d’un addendum, reconnaissant la nature évolutive de la construction des sols.
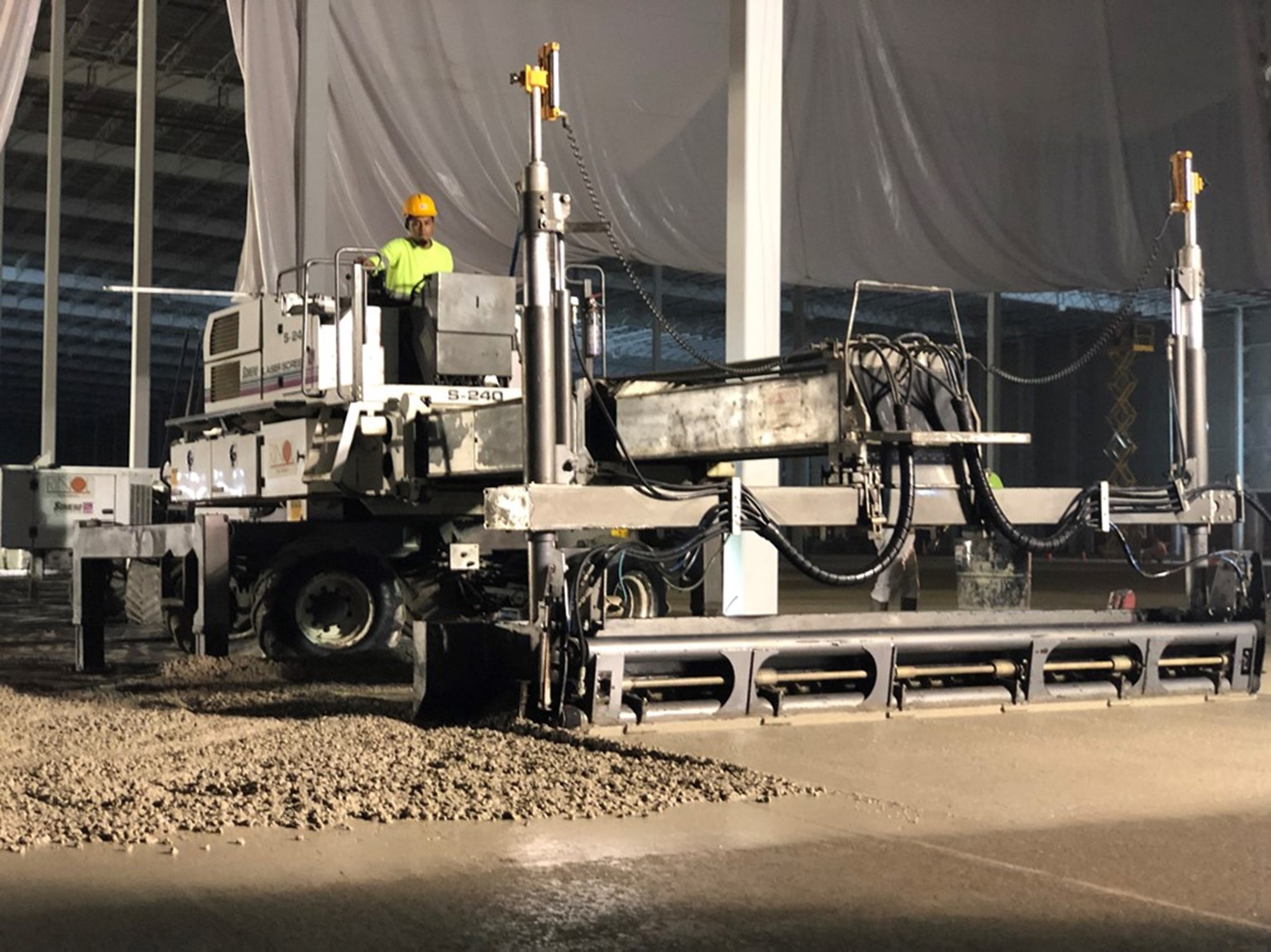
LA PRATIQUE AU QUOTIDIEN
Aujourd’hui, dans le monde entier, il existe de nombreuses normes définissant la régularité de surface, notamment : DIN-15185, DIN-18202, VDMA, EN-15620, ICI 05-TC / 09, NZS3114, etc. Bien que généralement adaptées aux fins pour lesquelles elles ont été rédigées, la plupart ont été biaisés en faveur d’une partie prenante ou d’une autre, que ce soit l’entreprise de dallage, les sociétés de contrôle ou les fabricants de matériel de manutention. La partie prenante rarement représentée est l’exploitant du bâtiment. L’ensemble du secteur est construit autour de la conformité contractuelle et non de l’optimisation des performances.
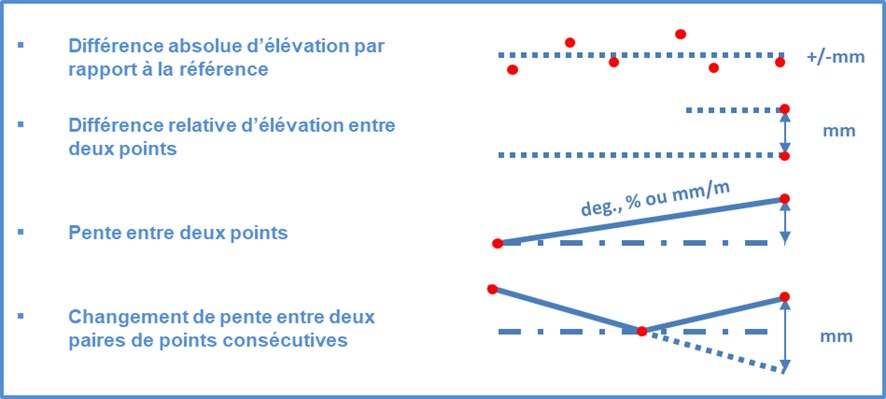
On peut soutenir que, selon le point de vue des parties prenantes, les fluctuations parmi les normes et les différences d’interprétation existent pour la protection contractuelle des intervenants. En particulier, le profil de la surface d’un sol évolue au fil du temps, soit par l’effet du tuilage au niveau des joints, soit sous la déformation de la dalle sous charge. Du point de vue de l’entrepreneur de sols industriels, la dalle a été exécutée selon les spécifications. Plusieurs semaines plus tard, du point de vue du fournisseur de chariots, les équipements ne peuvent pas rouler à pleine vitesse car le sol ne répond plus aux spécifications. Le moment choisi pour les tests est donc essentiel. On peut constater également que pour se protéger, certains constructeurs de matériel de manutention imposent des tolérances bien plus strictes à ce qui serait nécessaire, renchérissant ainsi le coût des dallages.
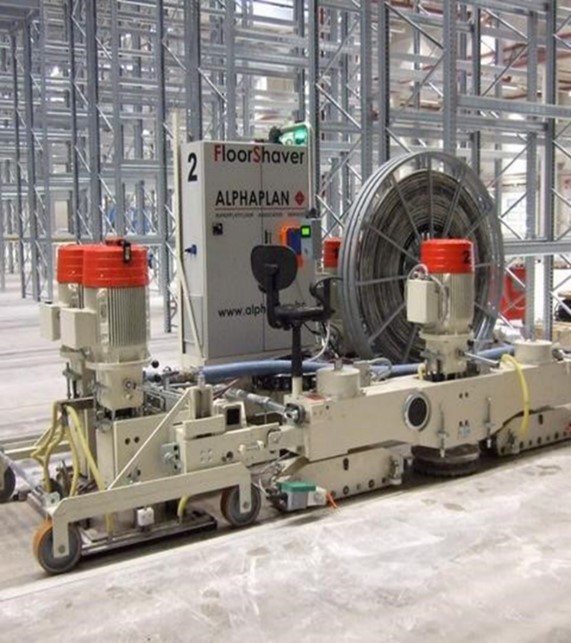
Bien que cela soit particulièrement critique pour les dallages à mouvement défini en allées très étroites, les déviations et erreurs peuvent finalement être identifiées et la rectification entreprise. Cela prend généralement la forme d’un ponçage de haute précision, bien qu’il existe également plusieurs options de revêtement. Si le ponçage est entrepris, ce doit être pour une bonne raison et pas seulement pour répondre aux spécifications à quelques fractions de millimètre près. Le ponçage peut conduire à affaiblir les propriétés mécaniques de la Surface par élimination partielle ou totale de la couche d’usure.
En ce qui concerne les sols industriels à trafic aléatoires (mouvement libre), les aléas sont encore plus grands. Naturellement, en raison de la nature laborieuse de la mesure et de la collecte des données, seul un échantillon est prélevé. On fait valoir que, statistiquement, cela fournit une bonne représentation de la qualité. La réalité est que pour les normes telles que ASTM1155, TR34 et DIN18202, moins de 2% de la Surface des dallages est échantillonné. Comme les emplacements exacts de ne sont pas strictement définis, on pourrait imaginer que l’entrepreneur peut influencer les zones où les lignes d’échantillonnage sont prélevées, assurant ainsi le respect des spécifications. De même, le technicien qui procède au contrôle a une certaine liberté pour sélectionner les secteurs pour démontrer que le sol n’est pas conforme.
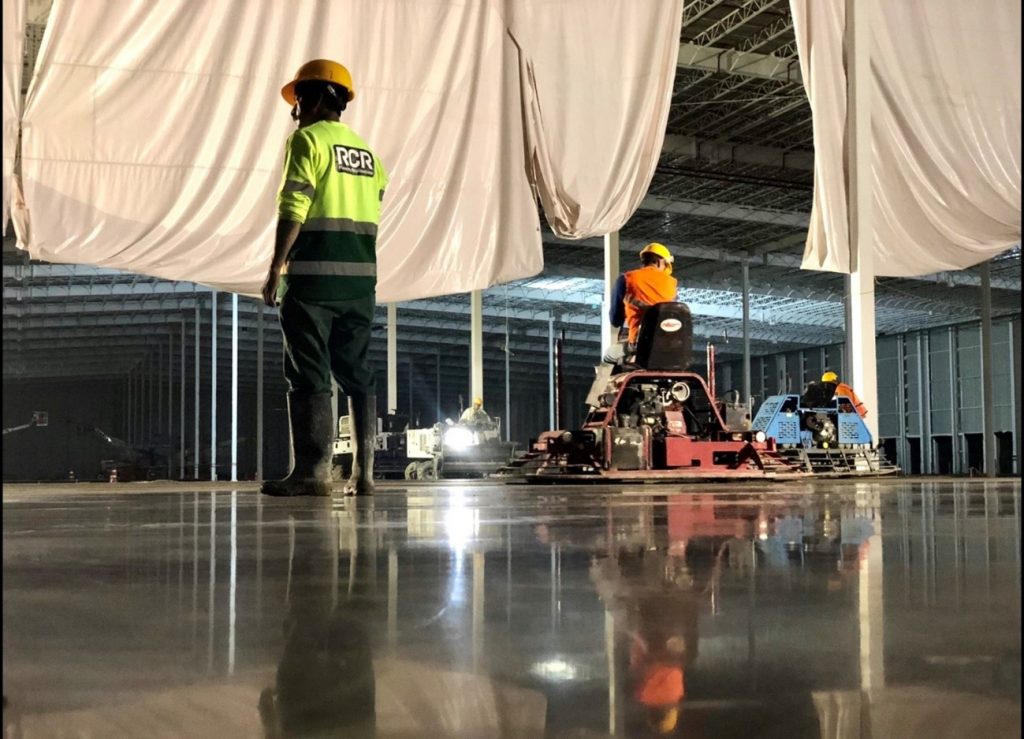
La grande question est alors de savoir où se situe la non-conformité et comment y remédier ? Généralement, le paiement est retardé ou bien des remises sont négociées. Certaines normes n’ont même pas de limite de 100%, définissant à la place uniquement le 95e centile. Techniquement, vous pourriez avoir des briques scellées sur le sol et toutefois passer positivement les spécifications, surtout si vous considérez qu’un très petit échantillon de mesures a été pris. Si un conflit survient et que le plancher doit être testé de nouveau, avec les effets combinés du temps, de l’emplacement des mesures, de la méthodologie, de l’instrument, de l’opérateur etc., la probabilité d’obtenir des résultats identiques est faible.
UN REGARD VERS LE FUTUR
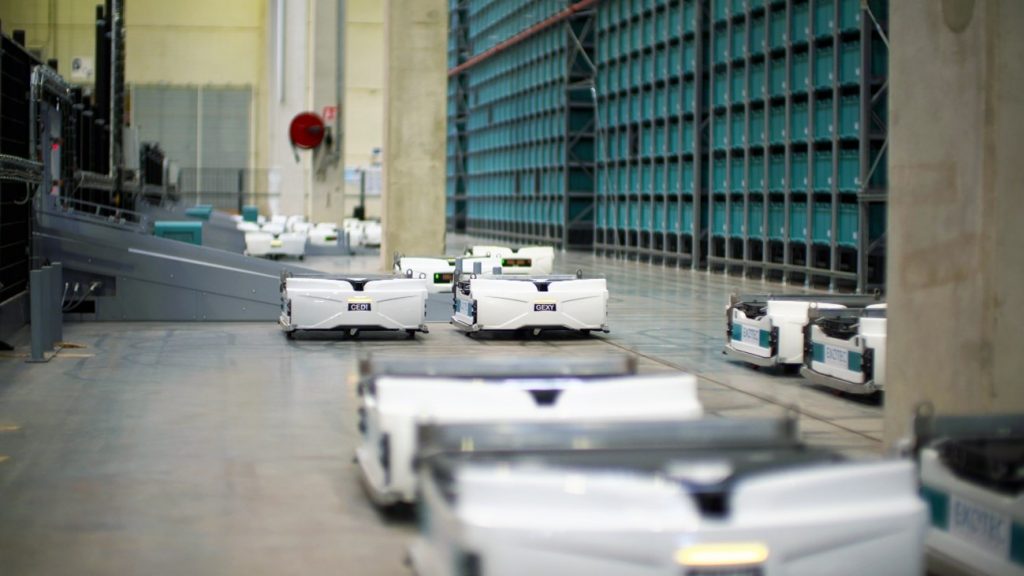
Tout en exprimant des réserves sur certaines normes et spécifications actuelles, elles ont généralement bien fonctionné tant du point de vue de la construction que du propriétaire ou de l’utilisateur du bâtiment. Cependant, avec l’automatisation croissante et le déploiement de robots dans les centres logistiques et les usines de fabrication, les exigences imposées au sol changent.
Ces robots ou chariots autonomes peuvent circuler n’importe où sur la dalle, soit sur une grille très dense prédéfinie ou selon un modèle aléatoire. La première conséquence est que la régularité de la surface du sol doit être constante sur toute la surface. L’utilisation de techniques de contrôle qui ne mesurent qu’un très petit échantillon pour vérifier la conformité est inappropriée. L’exploitant du bâtiment serait dans ce cas abandonné à son sort, à charge pour lui d’identifier et de corriger les zones à problèmes pendant l’exploitation. Cette approche génère des délais et des coûts énormes et inutiles. Il est désormais techniquement possible de déterminer le profil intégral de la surface d’un sol. La norme ASTM1155 a été mise à jour en 2014 pour permettre l’utilisation de scanners laser tridimensionnels pour mesurer les numéros F.
Il y a actuellement beaucoup de débats et de résistances à l’adoption de cette technologie. Premièrement, la méthodologie et l’équipement utilisés ont été mal transposés depuis l’univers BIM. Dans le monde des sols industriels, nous mesurons et rapportons avec une précision millimétrique, voire submillimétrique. Ceci peut être réalisé, mais uniquement en utilisant des scanners de haute qualité, avec des protocoles rigoureux pour la collecte des données.
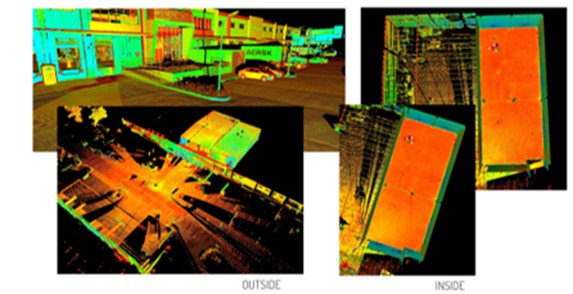
Tout aussi fondamental, il y a un manque considérable de connaissances et de capacité à interpréter les données. Les logiciels embarqués des stations laser peuvent faire illusion avec des fonctionnalités basiques mais ils ne sont pas à l’heure actuelle adaptés au traitement de milliards de points enregistrés par les instruments. Ceci encore, peut avoir des conséquences contractuelles graves. Prenons l’exemple d’un dallagiste engagé pour construire un sol conforme à FF45/FL35. L’entreprise générale, le bureau d’ingéniérie ou l’AMO du client peuvent charger un géomètre local de mesurer la conformité à l’aide d’un scanner laser.
Le résultat peut confirmer la conformité, mais le géomètre va publier un rapport contenant une cartographie en couleur du dallage. Cela peut faire impresión mais les zones rouges (hors tolérance) peuvent devenir une source immédiate de conflit. L’entreprise de sol industriel a livré ce qui était spécifié, mais le client s’interrogera sur les zones hors tolérance. N’oublions pas que la norme ASTM1155, même lorsqu’elle est mesurée à l’aide d’un scanner laser, ne nécessite qu’un très petit échantillon de données. L’interprétation peut donc être influencée par la personne qui paie pour la certification.
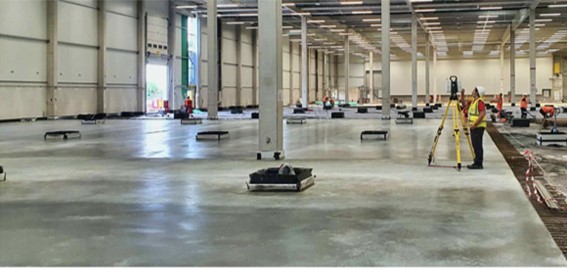
Suite à de nombreuses campagnes d’essais, et aussi à la suite d’expériences douloureuses, des progres importants ont été réalisés dans la compréhension des courbure et des profils d’ondulation de la surface du sol pour permettre un fonctionnement satisfaisant de divers types d’équipements de manutention autonomes (AGV, AMT). Aujourd’hui, cependant, une compréhension détaillée du comportement dynamique de ces véhicules fait défaut, et elle doit être caractérisée pour chaque type de véhicule. Une fois que cela est mieux compris, les vitesses de fonctionnement peuvent ainsi être optimisées et une plus grande efficacité obtenue. Aujourd’hui, grâce à des logiciels dédiés bases sur les technologies Big Data, nous avons la capacité de créer des cartes haute définition de la Surface. Nous sommes ainsi en mesure de pouvoir définir des spécifications basées sur les performances des équipements de manutention.
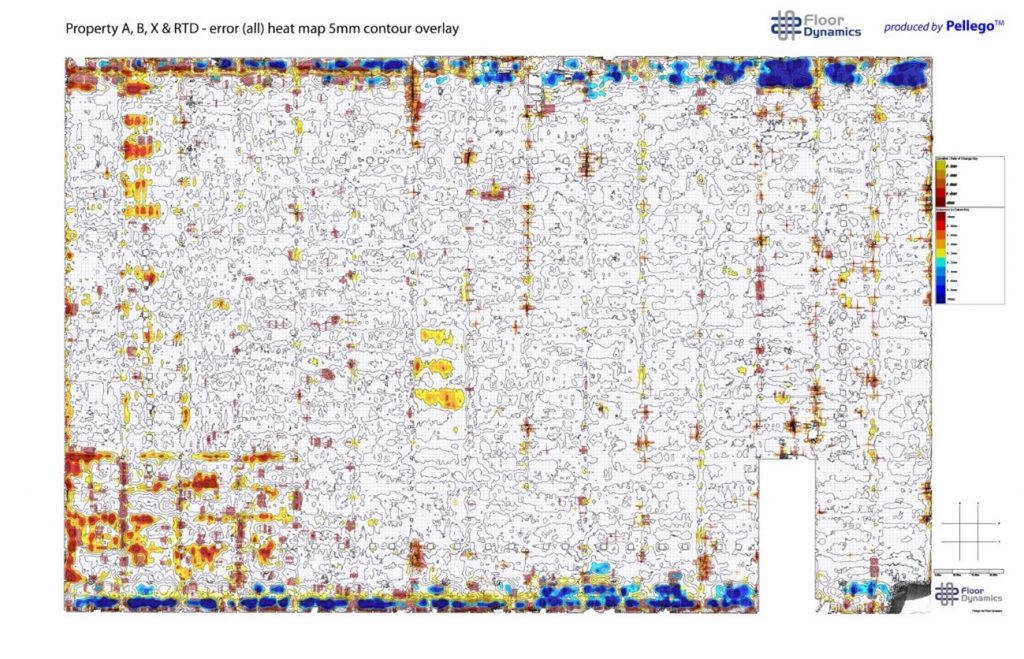
Dans le même temps, le secteur de la logistique automatisée doit apprendre que la construction des dallages pour les systèmes de véhicules autonomes ne nécessite pas de de spécifications ultra exigeantes avec des tolérances irréalistes. Cependant, elle nécessite une bonne régularité et une grande uniformité stable dans le temps et en tout point. Cela peut nécessiter l’adoption de différentes techniques non seulement pour le coulage, le nivellement et la finition, mais aussi la gestion de la qualité, la conception du mix béton etc. Les géomètres et les consultants doivent être en mesure de fournir des rapports d’une grande exactitude et fiabilité, basés sur des normes définies pour la collecte de données à l’aide de la digitalisation par laser. Les résultats doivent être cohérents et reproductibles. Enfin, les contrats doivent être établis entre toutes les parties, en se basant sur l’optimisation des performances du système de manutention et sur une méthode de rectification convenue en cas d’erreurs.
Il s’agit d’un nouveau chapitre dans l’histoire des sols industriels qui est en train de s’écrire.
Christophe Cortinovis (d’après l’article en anglais de Andrew Keen)
COO RCR Industrial Flooring