Artículos técnicos
10.05.21
Escaneo láser: ¿imágenes bonitas o mapeo de alta definición?
Parte 2. ¿REALIDAD O FICCIÓN?
En la época de las fake news, a menudo puede ser difícil determinar la verdad. Sin mirar los detalles, los titulares pueden estar sesgados para dirigir a la audiencia a una conclusión particular. Todo el mundo puede ser culpable de esto en cierta medida, en función de su sesgo y perspectiva. Sólo se convierte en un problema cuando se distorsionan descaradamente los hechos para engañar a la gente.
En un blog anterior, hablé de la percepción popular de que los escáneres láser terrestres no producen más que «imágenes bonitas» cuando se considera su uso para determinar el cumplimiento de las especificaciones de planicidad del suelo. Explicaba que, utilizando el equipo adecuado en un proceso estrictamente controlado, es posible recopilar datos de una calidad lo suficientemente alta como para producir mapas de alta definición de la superficie. Estos mapas pueden utilizarse para determinar la conformidad con las especificaciones. En este artículo, demostraré, utilizando datos concretos, lo que se puede conseguir, y se consigue, con Floor Dynamics a diario.
Benchmarking
Si se mide algo utilizando dos métodos diferentes y se obtienen respuestas distintas, ¿cuál es la correcta? ¿O ambas son erróneas? La realidad es que todas las mediciones tienen un grado de variación en la repetibilidad, incluso utilizando el mismo equipo y metodología. Esta variación se define como incertidumbre, que es una expresión de la dispersión estadística de los resultados. Se trata de un tema complejo y, para el propósito de este artículo, aceptaremos que, para cuantificar la calidad de una medición, es necesario compararla con un estándar de precisión acordado.
El proceso de Floor Dynamics para la elaboración de mapas HD utiliza múltiples instrumentos para garantizar la calidad de los datos. La Fig. 1 muestra un extracto de un informe de control de calidad, en el que se compara el valor de un punto determinado recogido mediante un TSL de grado de ingeniería con compensador de doble eje, una estación total de 0,5″ y un nivel digital con bastón invar de alta precisión.
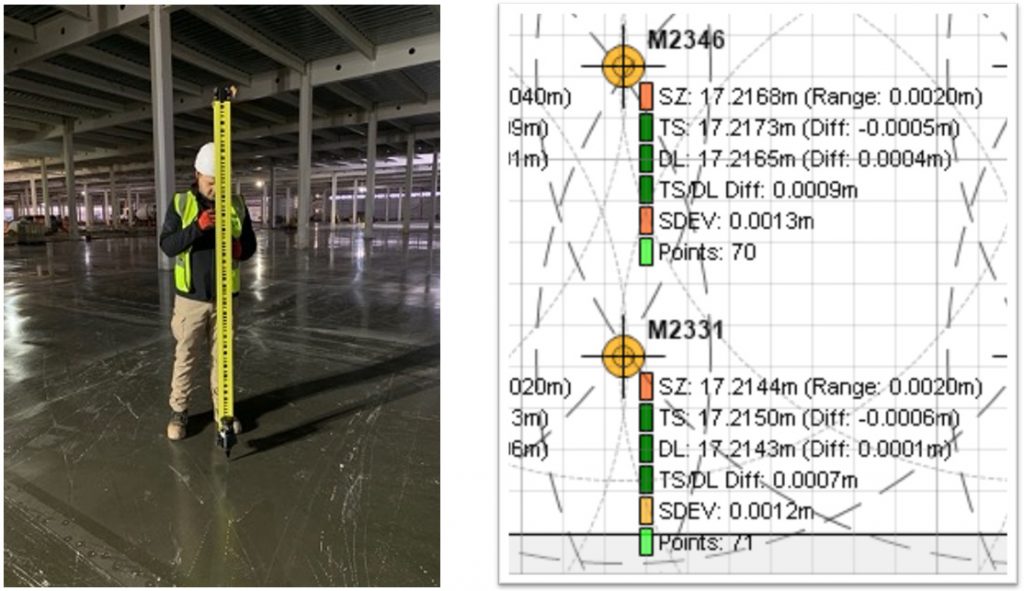
Las posiciones de los escáneres láser se determinan de manera que se puedan recoger suficientes datos bajo su punto ciego, desde lugares superpuestos. El registro preciso de estos escáneres individuales dentro de la red de control es vital. Cualquier problema con el registro será inmediatamente aparente, al ver los datos dentro de estas zonas muertas.
Pruebas independientes
Mientras que los procesos de Floor Dynamics proporcionan la validación de puntos discretos, recientemente tuvimos la oportunidad de participar en un programa de pruebas realizado por la BCTA en el Building Performance Hub de High Wycombe.
Se pidió a Hexagon, los fabricantes de instrumentos Leica, que inspeccionaran de forma independiente un área de suelo de 25 x 1,5 m utilizando rastreadores láser de última generación. Se estableció un sistema de coordenadas con un ATS960 y se midió un área «de referencia» con el ATS960 y un T-Scan 5. A continuación, se midió toda la superficie del panel de prueba con un ATS600 Laser Tracker y se comparó con el «punto de referencia». Se obtuvo una cuadrícula de niveles de 50 x 50 mm, con un total de 15.000 puntos discretos. La Fig. 2 muestra un mapa de elevación coloreado, a menudo denominado mapa de calor, de los datos. El rojo es alto. El azul es bajo.

Hexagon afirma que el ATS600 tiene garantizado el escaneo directo a una distancia de hasta 60 metros con una precisión de grado metrológico de 300 micras (cuando se utilizan SMR). Para comparar, Floor Dynamics inspeccionó el panel de prueba utilizando un Leica P40 en 4 posiciones. Se obtuvieron 10,5 millones de puntos lidar que se procesaron con nuestro software PellegoTM para producir una cuadrícula de niveles equivalente de 50 x 50 mm, cuyos resultados se muestran en la figura 3.

A primera vista, estos mapas de elevación no son ni mucho menos idénticos. De hecho, el uso de otros escáneres y procesos más sencillos dio lugar a mapas de aspecto similar. Para ver cualquier diferencia, los datos brutos de PellegoTM se restaron de los datos de ATS600 para obtener un mapa diferencial de valor Z (altura), que se muestra en la fig. 4.

Al analizar los 15.000 puntos individuales entre sí, se obtiene la siguiente dispersión, que se aproxima a 1, 2 y 3 s:
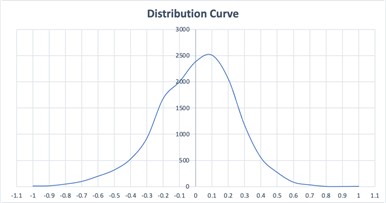
94.6% dentro de +/- 0.5mm
99.5% dentro de +/- 0.8mm
La losa de referencia tenía unas características específicas grabadas en la superficie, con el fin de seguir probando la topografía. El perfil de la superficie en 3D producido a partir del conjunto de datos de PellegoTM que se muestra en la figura 5, facilita mucho la visualización de los contornos en comparación con un mapa térmico. Además, se pueden distinguir los anillos reveladores de las cuatro posiciones del escáner. El más visible, a la izquierda de la imagen, es de +0,3 mm y está dentro de la incertidumbre de 0,8 mm indicada.

A continuación, el conjunto de datos de la medición fue procesado por PellegoTM para determinar la conformidad con las especificaciones. La Fig. 6 muestra la ubicación de los errores que quedan fuera del rango de curvatura de 6 mm entre dos pares de puntos consecutivos, separados por 300 mm. Aunque se calcula según una especificación personalizada, esto es esencialmente lo que estamos midiendo con la propiedad F de TR34, o la propiedad Ff de ASTM1155. Lo bueno de estos mapas de alta definición es que podemos calcular no sólo a lo largo de la cuadrícula, sino también perpendicularmente a ella, en toda la superficie. Los colores representan la gravedad del error.
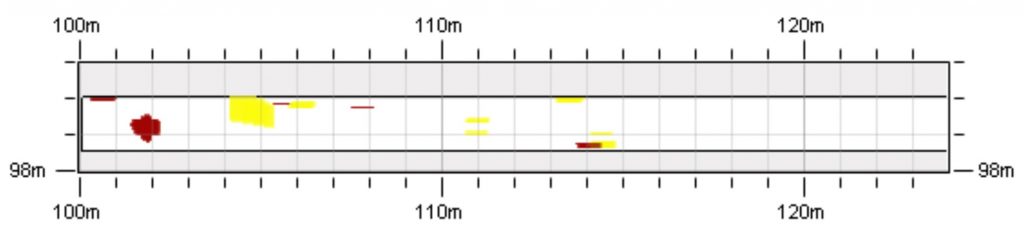

Curiosamente, los dos círculos situados a la derecha de la imagen no aparecen como un error. Esto se calculó adicionalmente de forma manual y se verificó mediante una inspección directa para confirmarlo. Todos los resultados muestran que esta zona se encuentra justo dentro de la especificación.
Este programa de pruebas, junto con los datos de control de calidad cruzados en cada proyecto inspeccionado, demuestra que la incertidumbre citada por Floor Dynamics de <0,8 mm no es inventada. La metodología es robusta y fiable y no da lugar a numerosos falsos errores positivos o negativos. Hay una advertencia. Como muestran las imágenes 3D, este proceso consiste esencialmente en fotografiar toda la superficie, incluyendo todo lo que hay sobre ella. El suelo debe estar limpio en el momento del escaneo. La basura, los montones de suciedad, etc., se incluirán y, en consecuencia, pueden dar lugar a falsos positivos (errores que no existen en la realidad). Los obstáculos más grandes pueden eliminarse durante el procesamiento, pero entonces no hay datos por debajo. Las mejores prácticas dictan la limpieza.
Incertidumbre compuesta
He leído y oído muchas críticas y alarmismos sobre la incertidumbre de metodologías como la utilizada por Floor Dynamics, especialmente en comparación con otros métodos de medición. Si se cita una incertidumbre de 0,8mm, entonces seguramente debe haber un efecto compuesto cuando se miden los errores de la tasa de cambio. Después de todo, hay 3 puntos distintos utilizados en el cálculo». En teoría, este es un argumento válido. Los datos del escáner láser sin procesar, seleccionando puntos lidar individuales, podrían dar lugar a estos problemas. Los escáneres láser tienen una firma de ruido y una tolerancia en términos de posición 3D y precisión horizontal y vertical. Tomar aproximadamente 200 lecturas individuales en una celda de 50 x 50mm, nos permite calcular la distribución de los datos. La comparación del valor Z asignado a la celda con otro instrumento de menor incertidumbre conocida, permite determinar cualquier sesgo en la medición o en el registro. La Fig. 7. demuestra el posible impacto compuesto de la incertidumbre en los valores Z individuales cuando se trata de calcular un error de tasa de cambio (curvatura). En este ejemplo, las líneas negras representan el límite de especificación de 10 mm. Las líneas roja y verde representan el peor escenario superior e inferior de incertidumbres compuestas de 1 mm. En teoría, este sistema podría informar de este error como 6 mm (potencialmente un falso negativo) o 14 mm (potencialmente un falso positivo).
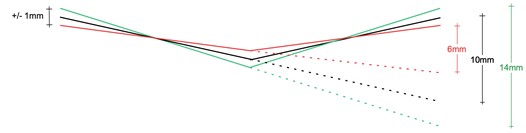
Fig 7. Efecto potencial de las incertidumbres compuestas en el cálculo de la tasa de cambio.
Cómo se comportan otros sistemas de medición
Durante el proceso de comprensión de las limitaciones de la tecnología de escaneo láser terrestre, hemos llegado a comprender mucho sobre otros dispositivos de medición utilizados en la medición de suelos industriales. Uno de los equipos con los que tenemos mucha experiencia es el nivel electrónico de pie, como el FACE Dipstick o el AXIOM 1155. Muy utilizados para comprobar la conformidad con varias normas, estos dispositivos son extremadamente precisos a la hora de medir la diferencia de elevación entre dos puntos discretos, es decir, los pies del dispositivo, normalmente espaciados a 300 mm. Los fabricantes indican precisiones del orden de 0,0125 mm. Aunque estos dispositivos son excelentes, fáciles y cómodos de usar, tienen inconvenientes. En primer lugar, son lentos. Esto limita la cantidad de datos que se pueden recoger de forma económica. Además, no tienen ni idea de su posición en el espacio tridimensional, por lo que no son fiables a la hora de informar sobre la elevación absoluta o la referencia al punto de referencia. Las versiones rodantes de este tipo de equipos, aunque son mucho más rápidas de utilizar, pueden ser propensas a acumular errores con la distancia.
Cuando se trata de medir según especificaciones de movimiento definidas, como la TR34 de la Concrete Society, las opciones son muy limitadas. La especificación está redactada de forma que las lecturas deben realizarse cada 50 mm a lo largo de la vía de la rueda. Esto dicta que se utilice un perfilador de suelo rodante, más conocido como perfilógrafo. Como el sistema Floor Dynamics traza los datos cada 50 mm, ahora podemos compararlos directamente con estos equipos. Es importante señalar que, al igual que los escáneres láser, no todos los perfilógrafos son iguales.
En un proyecto reciente, en el que se cuestionaban los datos de Floors Dynamics, tuvimos la oportunidad de hacer una comparación directa. Aunque no se trata de una prueba científica irrefutable, los resultados son interesantes. Es posible señalar con gran precisión una ubicación en un mapa de Floor Dynamics HD. Esto se puede repetir gracias a la conexión con la red de control establecida. No se puede afirmar con tanta seguridad que se sepa exactamente dónde se encuentra un recorrido del perfilógrafo. En recorridos de perfilografía de muestra de 150 m de longitud, trazamos un rastro equivalente a partir de datos que se encontraban dentro de un margen de +/-100 mm de la posición aproximada de la perfilografía.

La Fig. 8 representa la diferencia de altitud de los rodillos. La traza verde es del perfilógrafo y la roja, de PellegoTM. Teniendo en cuenta que las trazas pueden no ser exactamente de la misma ubicación, y que ambas metodologías tienen un grado de incertidumbre, hay una correlación sorprendentemente buena. Sin embargo, el final de la carrera, como se muestra en la figura 9, es una historia diferente
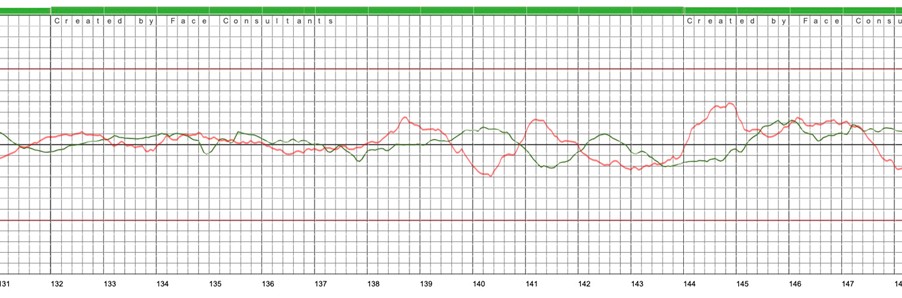
Estirando los datos de PellegoTM 1,2 m en el eje X, una vez más los resultados son extremadamente cercanos (Fig. 10.). Lo que esto sugiere es que el perfilógrafo ha viajado 1,2m más en 150m. Varios factores pueden explicar esto. Dejando de lado la calibración, o incluso una pequeña acumulación de material en las ruedas, un dispositivo rodante se desplaza cuesta arriba y cuesta abajo. Naturalmente, se desplazará más lejos que si estuviera en una superficie perfectamente plana. La retícula de datos emitida por PellegoTM está en un plano perfectamente horizontal. Este error puede no ser un problema si los datos se dividen en tramos más pequeños. Sin embargo, esto explica por qué no se pueden emparejar dos trazos de perfilografía si se mide en una dirección y luego se invierte la dirección, para tomar un segundo conjunto de datos.
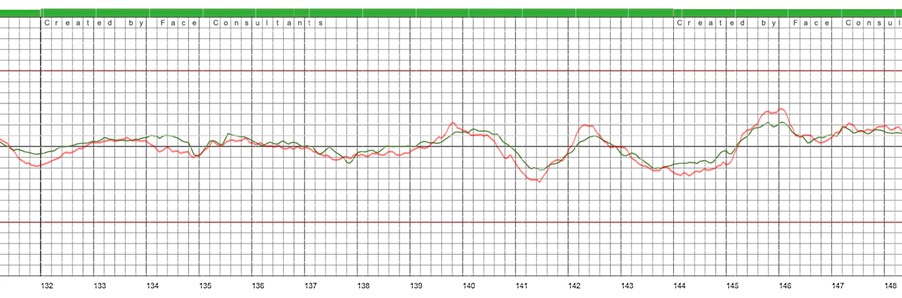
Algo más difícil de explicar es el fenómeno demostrado en la figura 11. Siempre que haya un cambio muy pequeño en la elevación, por ejemplo, una pendiente constante o un plano plano, hay una gran coincidencia entre los dos conjuntos de datos. Sin embargo, cuando hay un cambio rápido de elevación, ya sea en sentido positivo o negativo, puede haber una discrepancia significativa. En el peor de los casos, el perfilógrafo subestima el error en varios milímetros. Si el problema es el tiempo de respuesta del sensor de pendiente, se espera que el funcionamiento del perfilógrafo sea más lento para reducir este problema.
No es la primera vez que observamos esta discrepancia. Cuando construimos suelos de movimiento definido según la norma TR34 DM1, al no disponer de un perfilógrafo en la obra, nuestros equipos elaboran informes de calidad diarios utilizando una varilla de medición. Aunque esto se ajustaría a la norma EN15620, que es esencialmente la misma especificación, la norma TR34 prohíbe el uso de una varilla de medición, ya que no puede realizar lecturas cada 50 mm. Invariablemente, el estudio de la varilla de medición registrará peores resultados que un estudio de perfilografía llevado a cabo por una empresa topográfica de terceros al finalizar el proyecto.
Las causas de este fenómeno pueden ser varias. La explicación más probable es el tiempo de respuesta del sensor de pendiente. Con un perfilógrafo electrónico de suelo móvil, el operario debe detenerse, permitiendo que el sensor de pendiente se asiente, antes de poder registrar la lectura. Podría ser que con un instrumento rodante, como un perfilógrafo, el sensor no tenga tiempo de alcanzar su lectura completa antes de invertir la dirección. Por lo tanto, el error estaría infravalorado. Hay que destacar que los distintos fabricantes utilizan diferentes tipos de sensores.
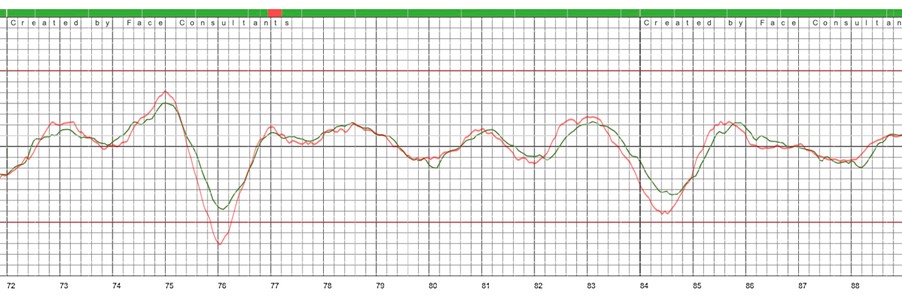
Resumen
Reconociendo que tengo un sesgo, he tratado de ser objetivo al escribir este blog. Existe una resistencia natural a la introducción de tecnologías disruptivas. La única manera de tomar una decisión informada es basándose en datos. Cuanto más persiste el debate, más detalles se descubren. No sólo en la confirmación de la nueva tecnología, sino también en las limitaciones de los métodos tradicionales. En definitiva, ¿son los datos capaces de ofrecer una información de suficiente calidad sobre la que tomar decisiones? En el mundo de las instalaciones logísticas automatizadas, Floor Dynamics está demostrando cada vez más el valor de mapear toda la superficie del suelo, y no sólo tomar una muestra estadística. Para las instalaciones que emplean la robótica, es necesario contar con características superficiales de calidad constante. Para saber si una zona del suelo necesita ser rectificada y dónde, se requiere una estrecha colaboración entre las distintas partes implicadas en el proceso de construcción. La forma en que se presentan e interpretan los datos puede causar confusión. Donde hay un error, no es donde hay que rectificar. Este es otro tema que trataré en un próximo artículo.
Andrew Keen
7th May 2021
Chief Services Office – RCR Industrial Flooring Group