Technical Articles
17.06.20
Using laser scanners to measure floor surface regularity
Question: Which 3D laser scanner should I use to measure floor surface regularity?
Answer: It all depends on what you want to achieve.
Laser scanners have been around for over 50 years. Their uses are many and they come in variety of types, ranging in price from a few hundred Euro for a simple handheld device, to 6 figure sums for metrology grade scanners. While drone based systems are becoming more common place, for the construction, we are normally referring to terrestrial laser scanner (TLS). These are ground based devices, mounted on a tripod or other fixed object.
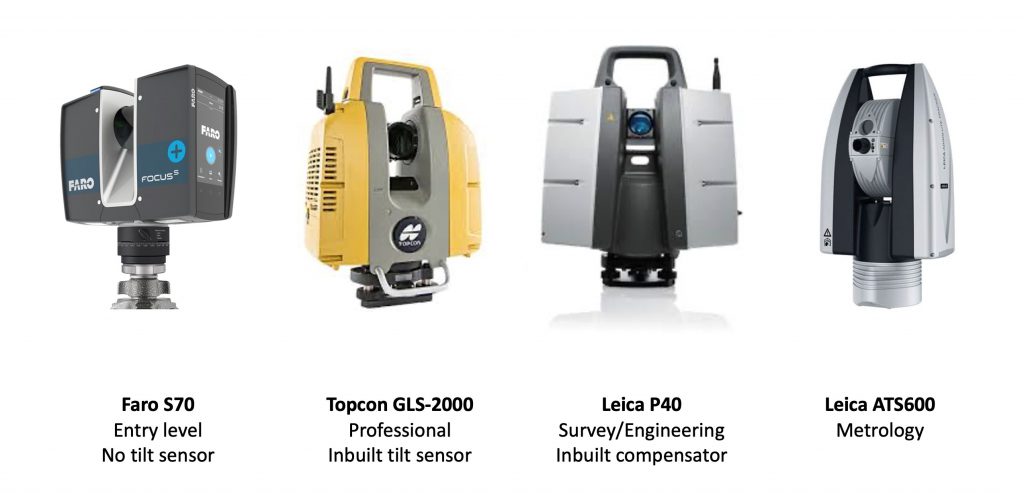
While commonly used in the construction industry, the use of terrestrial laser scanners for measuring floors is somewhat new and not something that they were specifically designed for. Broadly speaking, TLSs can be divided in to four categories – entry level, professional, survey/engineering grade and metrology. What sets them apart is accuracy, noise, range, ability to measure and/or compensate for movement while in use and portability. For BIM (building industry modelling), accuracy is not too demanding but portability, ease of use and price, maybe higher on the priority list. At the opposite end of the scale, if you need accuracy to 300 microns at 60 metres with very low noise (high repeatability), the price of a metrology grade laser is what you have to pay.
To give a broad picture of the surface profile, an entry level or professional grade scanner may be more than adequate. These instruments can be very useful for quick wet scans during the construction phase of the floor. However, to measure and collect data suitable for analysing floor surface regularity to sub millimetre level, such as is required to check conformance to current standards, only a survey/engineering grade scanner is suitable. A 3D scanner such as the Leica P40/P50 range, not only has the angular accuracy, range accuracy and low noise, but with an inbuilt compensator, tiny movements detected from vibration during the scan are automatically adjusted for. On a construction site, vibration is is an ever present risk.
So how does the accuracy of a 3D laser scanner compare to more conventional surveying equipment used to measure floor surface regularity, such as a walking or rolling floor profiler (Dipstick, etc) or profileograph? This can be a nightmare to try to determine. Firstly, ever scanner manufacturer seems to have their own method of quoting specifications. It is also not much better for proprietary surveying equipment. With some detective work, it is possible to draw a comparison between different instruments.
To measure elevation, vertical angular accuracy is the primary determining factor. For a Leica P40, this is quoted as 8 arc seconds (there are 3,600 arc seconds to 1 degree). A Dipstick is quoted as being accurate to 0.0125mm. However, a Dipstick or profileograph does not measure elevation change. It calculates this from the angle measured between two points by an inbuilt inclinometer. The following diagram explains.
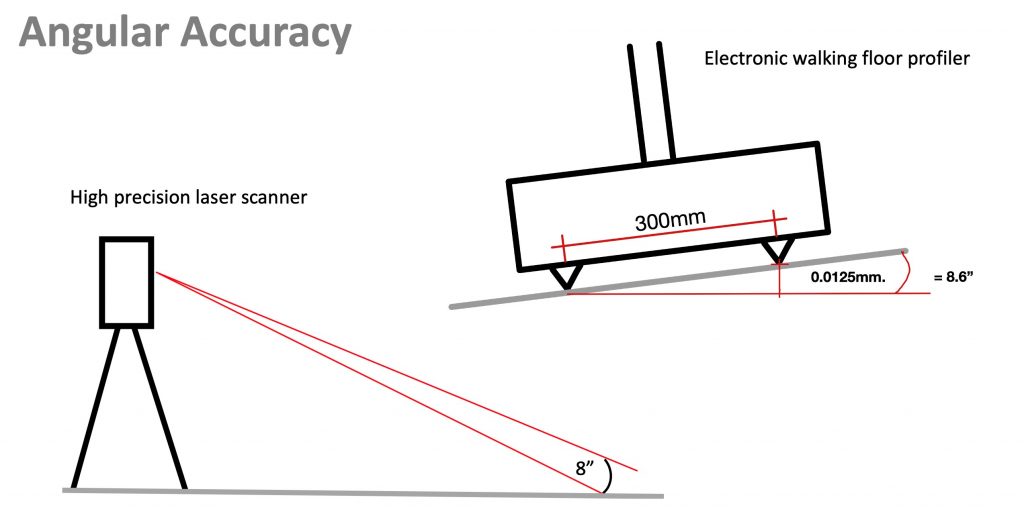
Both instruments are essentially equal. So far so good. However, the propriatory floor profilers have this potential error between 2 discreet points, 300m or 1ft apart. Every successive measurement has an equal potential for error, compounding the error over the length of the test run. A laser scanner, by contrast, has the same error over the distance of data collected. The potential elevation error will grow, the further away from the scanner but the angular accuracy remains the constant. As a consequence, to control elevation error, data is collected from multiple scan locations at typically 10m centres. To truly understand the reliability of the data collected by the different methods, we have to consider the uncertainty and confidence interval of the entire test process. That is a whole other subject for a future article.
Andrew Keen – CSO RCR Flooring Services